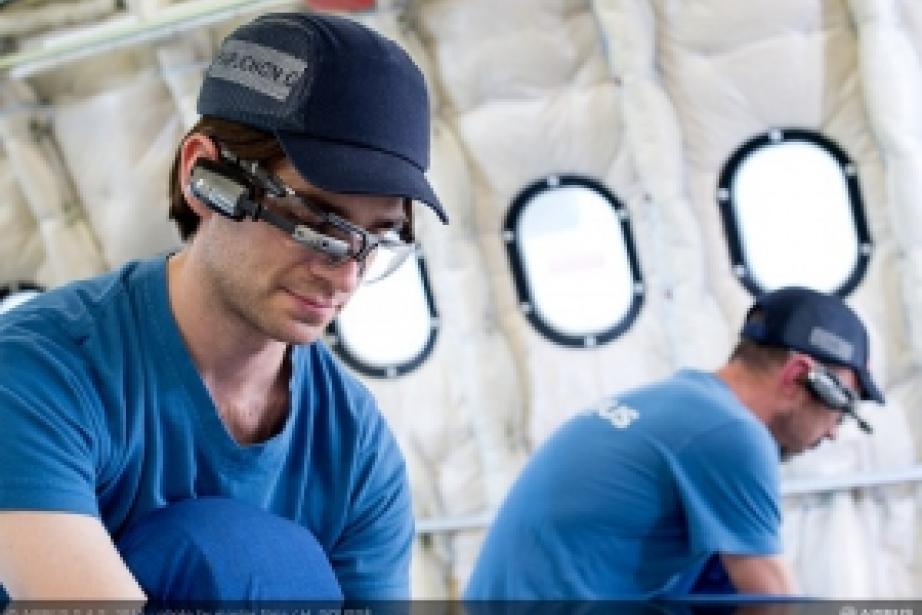
Lunettes connectées 3D sur la FAL de l'A330
« Chaque salarié d’Airbus peut contribuer à l’innovation » indiquait Yann Barbaux, le directeur de l’innovation d’Airbus le 7 octobre 2015 via la boîte à idée. Preuve à l’appui. L’avionneur avait invité tous ses salariés à St Martin lors de l’Innovation Showcase avec 10 ateliers d’innovations proposées par des collaborateurs et retenues par Airbus.
Le spectre était très très large avec le tsunami du numérique touchant l’embarqué, les technologies critiques de l’avion mais aussi tout l’écosystème de la production, des services aux clients, une application mobile destinée aux salariés d’Airbus en déplacement. Le numérique pousse Airbus à devenir plus agile pour implémenter rapidement les technologies. C’est aussi des opportunités pour raccourcir le chemin vers la certification des systèmes et aérostructures. Il y a aussi la place pour des innovations plus simples sans contenu technologique.
L’internet des objets à bord
L’introduction de l’internet (IoT) des objets dans les process d’Airbus va contribuer à créer de la valeur partout dans les chaînes de production, la logistique, le management…et à bord des avions. Exemple dans les cabines avions, en reliant des objets porteurs d’étiquettes RFID (à 18 kbs par radio), via une antenne dédiée à l’IoT (implantée dans la structure), la présence des ceintures de sécurité dans chaque siège, l’état de santé de systèmes est vérifiable automatiquement sur un écran de contrôle, l’anomalie apparaît en rouge. On imagine les gains de temps pour les compagnies aériennes, de sécurité, la possibilité de contrôle à distance. Ces applications IoT devraient être industrialisées dans les deux prochaines années. Airbus a dénombré près de 3000 cas d’application sur une A350. Au total l’IoT représentera plusieurs millions d’euros de bénéfices supplémentaires pour l’avionneur en reliant le physique et le digital.
Les lunettes connectées sur la FAL A330
Zéro erreur et l’inspection automatisée soit plus de qualité et des gains de temps, tels sont les avantages de l’utilisation des lunettes connectées, Smart Glasses, qu’Airbus a évaluée sur la FAL A330 pour les opérations de marquage réalisées sur les structures par les compagnons. « On divise le temps par 6 en sécurisant à 100% ces tâches fastidieuses et répétitives » relatait Stéphane Ripoll. Après le chargement par code barre, le compagnon choisit par commande vocale le rail sur lequel il va travailler et la localisation de la zone à marquer est indiquée en réalitée augmentée par les lunettes. Cette innovation sera déployée sur la FAL A330 en 2016 et à terme sur d’autres FAL Airbus.
Les collets en papier pour les harnais de l’A320 !
C’est une idée simple proposée par un compagnon travaillant à Brougthon chez Airbus UK spécialisée dans la voilure pour remplacer les attaches provisoires en plastique des câbles sur les harnais par des collets en papier détachables à la main sans faire appel à une pince. Avantages : plus de risque d’endommager les câbles, gain de temps. 800 000 colliers sont enlevés chaque année sur les A320. Un brevet est déposé et Airbus a contacté un industriel.
Quelles sont les pièces destinées à la fabrication additive ?
La fabrication est devenue un sujet stratégique chez Airbus qui a développé un logiciel GEOsearch servant à identifier si une pièce est ou non susceptible d’être produite en impression 3D. La première version est entrée en service en juin 2015. Le logiciel est capable d’analyser 130 000 fichiers de pièces en moins d’une minute ! C’est idéal pour les derniers programmes réalisés en maquette numérique (l’A380, l’A400M, l’A330 en partie…). D’autres solutions complémentaires analysent les possibilités d’assemblages. Airbus a créé un plateau spécifique sur l’impression 3D avec la volonté d’aboutir rapidement pour saisir toutes les opportunités de gain. Le travail s’effectue en liaison avec ses fournisseurs sur un sujet complexe qui peut rabettre les cartes.
Un compacteur d’ordure embarqué
Le Vacuum Trash Compactor imaginé par un jeune ingénieur d’Airbus Marc Spille, réduit la masse des ordures collectées à bord de 50% en utilisant la différence de pression de l’air. Ce compacteur pèse à peine 25 kg contre une centaine de kilos pour les systèmes actuels dotés de process électromécaniques. Un démonstrateur sera testé en 2016, les compagnies aériennes sont intéressées pour diminuer les coûts. Des fournisseurs ont été contactés.
Le pilotage des CoBots
Airbus développe une chaine numérique pour le pilotage des CoBots, les robots « collaboratifs ». L’idée est de programmer rapidement des robots sur les chaînes d’assemblage à partir de la maquette numérique, des cotes des pièces et l’opération à réaliser, en fournissant la programmation des trajectoires du cobot. Une solution industrialisée est envisagée en 2016-2017. C’est un outil générique adapté à tous les éditeurs et marques de robots.
Simulateur de cockpit
Pour tester rapidement de nouvelles configurations et fonctions de vols, Airbus Innovation a développé, le Virtual Reality flight Simulator, un simulateur de cockpit. Les systèmes sont reproduits en réalité augmentée que le pilote voit à travers son casque 3D assis sur son siège. Il manipule virtuellement les commandes en bougeant son bras, la manette de gaz reste réelle. C’est un outil pour réduire les coûts des études et le temps de développement amont sans développer un démonstrateur physique.
Travel App : faciliter les voyages d’affaires des salariés
L’application mobile Travel App facilite les rencontres et la localisation des salariés d’Airbus en déplacement. 1/3 des airbusiens voyagent 5 fois par an en moyenne. Cette App permet entre autres de partager des voitures de location, de localiser ses collègues à l’étranger si la fonction « around me » est autorisée par l’utilisateur, de se créer un réseau, de chatter…Cette App en phase de test a vocation à être utilisée par tous les salariés d’Airbus Group (140 000 salariés dans le monde).
Capteurs wireless pour les essais avions
En éliminant les réseaux de câbles nécessaires aux capteurs de mesure qui sont installés au sol ou sur les avions pour les essais avions, Airbus veut réduire les coûts, les délais de déploiement et le poids. Sur avion les solutions et composants de l’IoT sont envisagées pour relier les capteurs disséminés sur l’avion aux systèmes de contrôle. Airbus ajoutera de nouveaux capteurs, des jauges de contraintes, de température… sans câblage. L’industrie électronique et des capteurs est en train d’adopter le sans-fil. Il faudrait 5 à 10 ans pour supprimer le câblage des quelque 6000 capteurs utilisés pour les essais avions.
Recherches sur les aérostructures
Le projet européen Smart Intelligent Aircraft structures SARISTU vise à introduire entre 2020 et 2030 de nouvelles technologies sur les structures de l’avion pour améliorer les performances aérodynamiques, diminuer le poids et le coût de la maintenance. Airbus a piloté ce projet qui a recensé 16 innovations potentielles par exemple pour contrôler les déformations des matériaux, les turbulences, en utilisant des nanocapteurs dans les structures, des matériaux à mémoire de forme, sur des winglets, ….
Faciliter l’émergence des idées
Airbus a déployé des supports pour faciliter l’émergence de l’innovation en interne avec la boite à idée électronique visible par tous les collaborateurs, 120 correspondants dédiés, une vingtaine chargés d’approfondir et sélectionner les meilleures idées, le test rapide des prototypes, la création du BizLab à Toulouse, à Hambourg, à Bengalore, lorsque le projet est suffisamment mature pour être porté par une mini startup….
Article diffusé par Jean Luc Bénédini le 01/11/2015