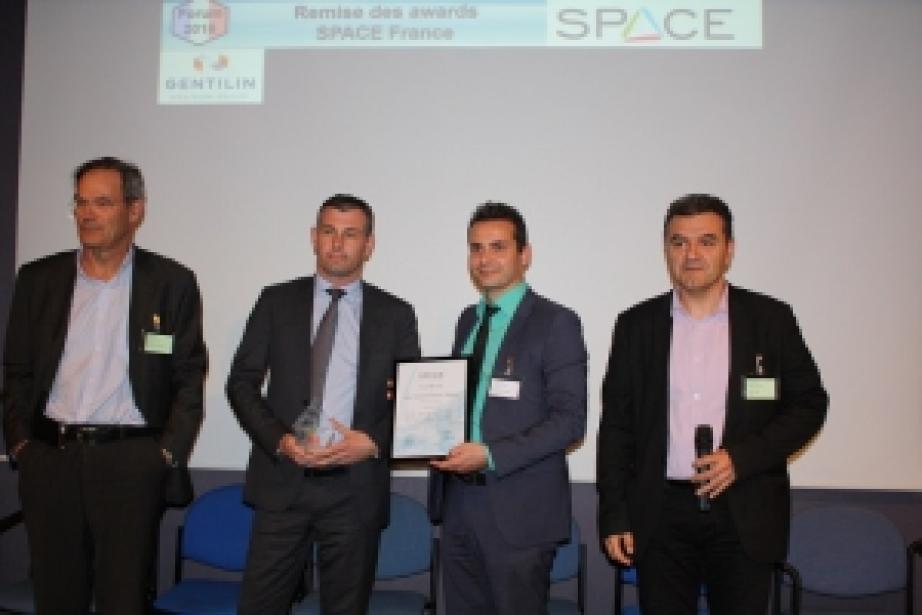
de g à d : François Bertrand, président de Space, Frédéric Gentilin, président de Gentilin, Nicolas Guillaume, directeur industriel de Gentilin, Guy Soulié, chef de projet chez Space
Descendre en dessous des 1000 PPM, le nombre de défaillances par millions de pièces produites est atteignable par la supply chain aéronautique. Preuves à l’appui lors du Forum France 2016 de Space organisé le 12 avril dernier à Colomiers. Plus d’une centaine de donneurs d’ordres et sous-traitants impliquées dans les actions d’amélioration de la performance industrielle, collectives ou individuelles de Space, étaient présents. C’est un sujet chaud avec la montée en cadence des programmes A320neo, A350. Pour baisser la non-qualité durablement, de nouveaux outils de management comme le QRQC, (Quick response quality control) ont fait leur apparition chez les clients et les fournisseurs, dans les ateliers à la source des défaillances.
L’idée c’est de détecter au quotidien, traiter rapidement et durablement la cause des défauts.
Les donneurs d’ordres à la manœuvre
Exemples chez les donneurs d’ordre qui ont lancé des chantiers en interne et en collaboration avec leur supply chain. Stelia traite avec près de 200 fournisseurs majeurs qui lui livrent 60 000 pièces par semaine environ. Tous fournisseurs confondus, 4500 PPM étaient enregistrés en 2015 pour un coût de la non-qualité de 4,5M€. Lorsqu’un problème est détecté avec une pièce provenant d’un fournisseur, une action est déclenchée avec le QRQC dans les 24H. Avec la méthode de résolution 8D, cet équipementier analyse les causes profondes, mène des plans d’actions correctives et préventives. L’an dernier Stelia a ainsi pu réduire de 4200 à 1800 PPM les non conformités pour la voilure de l’ATR. Liebherr Aerospace a déployé l’an dernier une quinzaine de QRCQ à la fois en interne et chez trois fournisseurs. Le nombre de défauts est passé de 7000 PPM en 2006 à 2800 PPM en 2015 pour un objectif de 1000 en 2018. Le temps moyen de traitement des non-conformités est de 43 jours avec un objectif de 20 jours. Avantages : « Nos clients ne paniquent plus car nous avons le QRQC en place. Les fournisseurs sont formés. Cela facilite la gestion des crises et entretient la motivation de nos équipes » indiquait Fabien Petit, le directeur qualité de Liebherr Aerospace. Chez Ratier Figeac (Propeller System avec trois sites à Figeac, 1250 personnes, Casablanca, 110 personnes et aux USA, 50 salariés), on applique la méthode ACE de la maison mère, le groupe américain UTAS dupliquée partout dans le monde. Parmi les outils figurent les Cliniques Qualité depuis 2005, implantées au coeur des ateliers de Ratier Figeac. Sept entités fonctionnent au quotidien à Figeac, en triant l’information, en trouvant les causes racines des défauts, en déployant des systèmes anti-erreurs, en associant les opérateurs concernés. Le nombre de PPM chez les fournisseurs est passé de 5000 en 2005 à 300 PPM en 2015. Entre temps le panel s’est réduit de 450 à 300 fournisseurs tout en multipliant par trois le volume achat traité. Chaque mois, les fournisseurs reçoivent le scorecard présentant les résultats PPM et OTD. Ratier Figeac pilote une grappe Space de 7 fournisseurs. « C’est un travail sur le long terme, année après année » relatait Patrick Derbois, le directeur achat et supply chain.
La chasse au PPM chez les fournisseurs
Dans les ateliers chez les fournisseurs, la chasse au PPM s’est intensifiée. Chez le fabricant ariégeois Recaero (580 salariés, 43 M€ de CA), le QRPC a été déployé avec le soutien de Turbomeca. C’est devenu un rituel quotidien avec la prise en compte des indicateurs de SQCDP (Sécurité, Qualité, Coûts, Délais, Personnel), une enquête déclenchée à j+1 avec une fiche de résolution de problème. L’outil est en place sur les sites de Verniolle et Mirepoix et sera adapté pour l’unité indienne. Exemple cité sur une tuyauterie trop longue de 2 mm dont le défaut n’avait pas été détecté malgré plusieurs étapes de contrôle. Après enquête (5P), le contrôle d’outillage défectueux a été réaménagé. Avec le QRQC, Recaero a réduit le nombre de retouches, d’arrêts de production et amélioré ses performances OTD et PPM. Cette entreprise a reçu le trophée Fournisseur Safran en 2015.
Filiale du groupe We Are Aerospace (Farella, Chatal, Ace, Prismadd, Armor Meca, 1000 personnes, 10 sites), Espace à Muret, spécialiste de la tôlerie fine, a développé une démarche qualité avec la mise en place du QRCQ, des indicateurs qualité à tous les stades. Dans le cadre de la grappe Stelia, ce sous-traitant est en train de fortement baisser la non-qualité. Chez Cazenave (100 salariés, 16 M€ de CA) à Pau, spécialiste en rectification et fraisage, les problèmes sont traités sous 48h, le nombre de PPM est passé de 3723 en 2014 à 2080 en 2015 avec un objectif de 1000 PPM. Les progrès sont très sensibles chez tous ceux qui sont impliqués dans Space. « Aujourd’hui nous détectons, nous traitons et nous prévenons les non-conformités dans l’amélioration continue. Depuis quelques mois, on ne contrôle plus les pièces, on évalue les process » indiquait Philippe Parsoire, le dirigeant de Freyssinet Aero Equipement à Couffouleux dans le Tarn. Il y a bien sûr un coût de gestion en introduisant ces outils mais la question est vite tranchée. « Le vrai risque c’est de se faire sortir du marché ». Le point névralgique pour réussir souligné par tous les intervenants, visait le partage de l’objectif stratégique commun, du haut en bas de l’échelle. Par exemple en donnant du sens aux actions des opérateurs avec des rituels, avec une culture non punitive, qui génère des opportunités de progrès.
Gentilin : Award Space France 2016
Gentilin a reçu l’un des deux awards Space France 2016. Cette entreprise de mécanique de précision de Launaguet membre de Nexteam Group, a anticipé la montée en cadence dès 2012 pour accroître ses performances industrielles en s’impliquant dans Space, en adoptant le MRP2, avec des outils d’analyse de charge/capacité, de planning machine, en développant des indicateurs qualité dans chaque service, des rituels de contrôle, la formation…L’OTD a par exemple pour les pièces série a évolué de 92% en 2014, 94% en 2015 et 98% en 2016.
Article diffusé par JL Bénédini le 01/05/2016