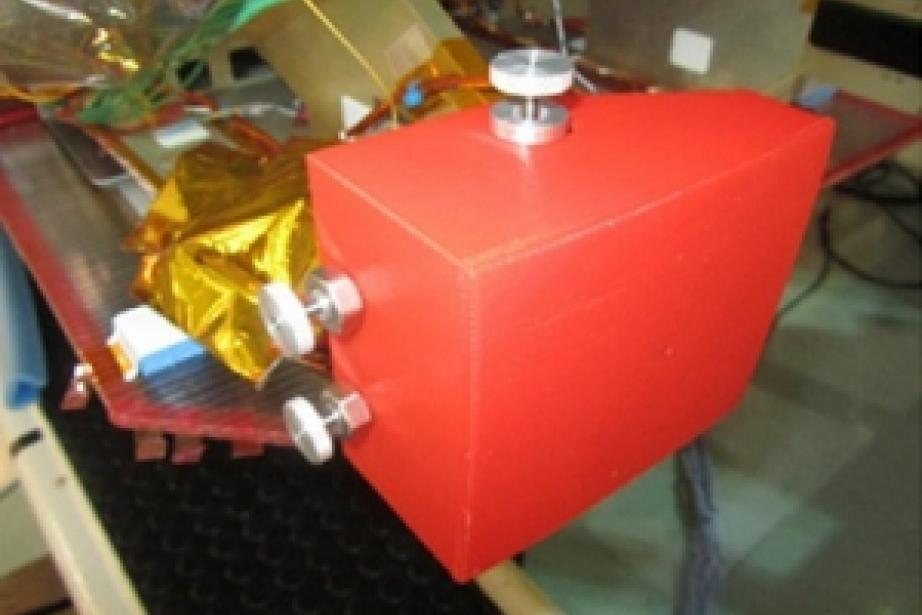
Protection de satellite
La fabrication additive est déjà passée au stade industriel chez Airbus Defense and Space. Dans l’impression 3D de matière plastique, de polymère, les 4 machines sur le site du Palays à Toulouse fonctionnent jour et nuit. Les applications concernent des pièces relativement simples avec peu de contraintes mécaniques, pour l’outillage au sol par exemple utilisées dans la protection des satellites, la réalisation de maquettes pour les bureaux d’études. Moins cher et bien plus rapide, la décision de s’équiper a été prise rapidement. « Au bout d’une semaine d’impression, on rentabilise la machine » relate Claude Lorda, responsable de l’innovation industrielle, avec des coûts raisonnables de 600€ pour les premières générations jusqu’à 6 ou 8k€ aujourd’hui. Sur les sites anglais de Portsmouth et Stevenage, des machines identiques ont été installées. La prochaine étape, largement plus ambitieuse, vise le vol en orbite de pièces plastiques. Elles devront passer entre autres les tests de vide thermique chez Intespace. Airbus Defense and Space participe au projet de R & D piloté par le Cnes pour qualifier un polymère en vol destiné à des pièces peu sollicitées. Il s’agit notamment de vérifier la tenue aux radiations, la non prise en charge électrostatique du matériau, la neutralité vis-à-vis des composants des satellites.
Avec le métal, l’ALM est déjà une réalité en orbite avec un élément de support d’antenne en titane sur le satellite Atlantic Bird 7 lancé en 2011. L’économie de matière première, la possibilité de fabriquer des pièces très complexes, la réduction de la masse, les gains de temps sur le planning général d’un programme satellite en fabricant les pièces très tardivement, sont autant d’atouts cités. «Nous travaillons sur des pièces à la géométrie complexe qui n’ont pas de rôle structural important par exemple en créant des nœuds thermiques sur des réseaux de caloducs en aluminium qui facilitent le transfert thermique, que l’on se sait pas réaliser autrement qu’en ALM, ce qui permet d’augmenter sensiblement l’efficacité thermique et donc la masse globale explique Bernard Gergonne, expert en design mécanique. Pour les pièces à fortes contraintes, le travail d’investigation se poursuit, le coût des essais devient ici un élément clé dans le calcul économique. Pour la fabrication, Airbus Defense and Space a fait appel à la sous-traitance extérieure, chez Poly-shape, ou d’autres fabricants français ou européens. Les futures pièces réalisées en ALM qui voleront sur satellite en 2016-2018 concerneront des protections anti-météorites, des supports de senseurs. A noter que l’ALM pourrait prendre une place significative dans le développement d’Ariane 6 confiée à Airbus Safran Launchers.
Article diffusé le 23/12/2015 par JL Bénédini