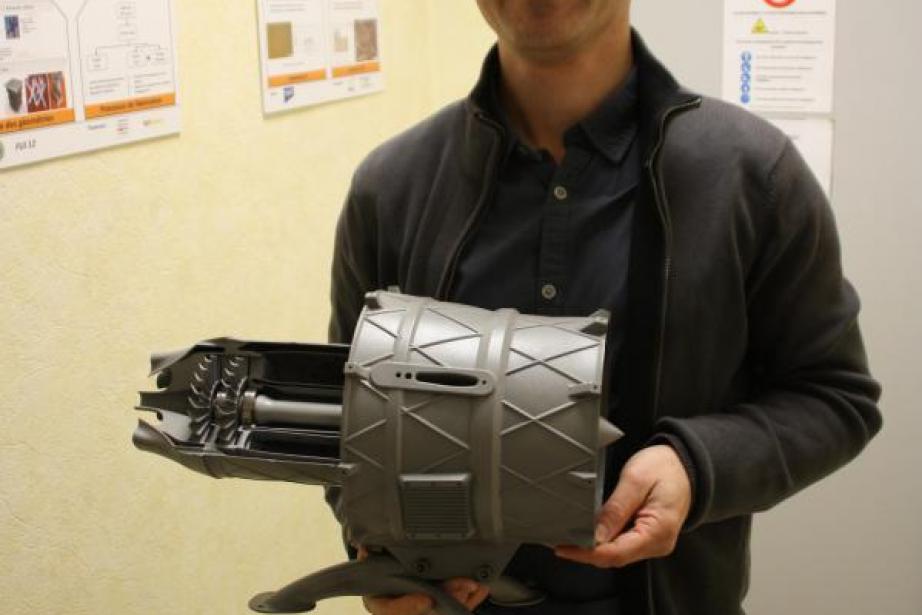
Arnaud Votié, directeur de la R & D de Fusia tenant une turbine entièrement réalisée en fabrication additive
Depuis la fin 2016, Fusia est qualifié par Safran Power Units en fabrication additive par fusion laser de poudre métallique sur les alliages base nickel. Cette startup toulousaine, lancée en 2011, installée à proximité de sa maison mère, la société de mécanique Estève à Montaudran, fait partie des quelques sous-traitants en Europe que Safran Power Units a qualifié pour ce nouveau procédé spécial. Une étape cruciale pour engager la montée en cadence industrielle ciblant la fabrication de pièces complexes avec une prestation complète.
Il aura fallu cinq ans de travail acharné pour atteindre le niveau d’exigence d’un équipementier aéronautique et démontrer que le procédé et l’organisation de l’entreprise étaient bien conformes.
« Tout a été finalement très rapide car on partait de quasi zéro il y a cinq ans. Nous avons progressé ensemble avec nos clients et partenaires dans la connaissance et la maîtrise progressive des matériaux et des procédés » relève Arnaud Votié, directeur de la R & D de Fusia. La stratégie a été de mener de front à la fois, la R & D sur les sujets critiques, des actions sur la qualité et l’industrialisation. Les échanges ont et sont particulièrement intenses avec les équipes de Safran Power Units (ex Microturbo) à Toulouse, Safran Aircraft Engines ou Technofan, basés sur une confiance mutuelle. Les bases de données, les référentiels et les procédés ont avancé de concert vers la maturité technique. Ces travaux débouchent en ce début d’année sru la production en série de pièces. D’autres alliages pourront être rapidement ajoutés à la liste (titane, alu…). La courbe d’apprentissage est très loin d’être épuisée. Fusia est engagée dans une dizaine de projets de R & D collaboratifs avec de nombreux partenaires industriels, bureaux d’études et laboratoires.
L’ingénierie simultanée des pièces avec les bureaux d’études a été renforcé ainsi que le co design pour parvenir à l’excellence plus rapidement. Contrairement à l’idée retenue par le public d’une technologie no limit géométrique illustrée par des designs très futuristes, il existe bien des limites topologiques et des contraintes de fabrication propres à la technologie. « Il peut y avoir des gains sur plusieurs fronts » indique Arnaud Votié avec la réduction de la masse, du nombre d’assemblages avec l’intégration de fonctions et donc de contrôles, la diminution des délais, la gestion des encours…. C’est le bilan économique global qui va entraîner ou non la décision de passer à la fabrication additive. On est loin d’une machine presse bouton !
Plusieurs types de pièces des zones chaudes des moteurs sont concernés. Des zones pièces plus contraintes d’un point de vue thermo-mécanique sont également visées à terme et des évolutions significatives sont attendues grâce au redesign d’ensembles plus complets.
Certaines pièces de série , volent par exemple sur des hélicoptères de l’armée canadienne servant de support pour des caméras embarquées. En 2017-2018, le Cnes prévoit de mettre en orbite le satellite Taranis avec un support de capteur fabriqué par Fusia dans le cadre du projet ALMIA.
Deux machines tournent aujourd’hui jour et nuit dans l’atelier Fusia à Toulouse, déposant plusieurs dizaines de microns de poudre pour chaque couche, créant la pièce en quelques heures. Les très bonnes performances en répétabilité permettent d’envisager sans problème la série avec des précisions de l’ordre du dixième. Les pièces sont ensuite finies dans l’atelier d’usinage d’Estève situé à proximité. « Nous assurons une prestation complète avec le maximum de valeur ajoutée ». En parallèle de la préparation à la qualification Safran Power Units, Fusia a décroché les certifications ISO9001 et EN9100. A Toulouse, 5 à 6 salariés sont employés chez Fusia et une quinzaine au total avec l’activité générée chez Estève (85 personnes). Mais Fusia c’est aujourd’hui un groupe, Fusia Groupe, avec une entité sœur au Canada à Montréal lancée par Cyrille Chanal (une machine), FusiA impression 3D Inc et une société d’usinage locale HRT Industries Inc. Si des deux côtés de l’Atlantique, chacun travaille avec son écosystème économique local, le savoir-faire est partagé.
Associé dans SOFIA avec Fives et Michelin
L'ambition du projet collaboratif SOFIA signé en novembre 2016 est de concevoir une nouvelle machine très performante en développant toutes les briques technologiques de la fabrication additive métallique : une gamme de poudres, les machines, les procédés. Il est piloté par la co-entreprise Fives Michelin Additive Solutions associée avec Aubert & Duval, ESI Group, Fusia Groupe, Safran, VOLUM-e, Zodiac Aerospace et des partenaires académiques, le CNRS, Centrale Supelec, Centrale Nantes, l’Ecole Polytechnique, ENS Paris-Saclay (ENS Cachan), l’Université Paris Diderot, l’Université Paris-Sud, l’Université Pierre et Marie Curie - Paris VI.Un programme sur 6 ans mobilisant 50 M€ soutenu financièrement par BPIfrance au titre de Projet de recherche et développement Structurant Pour la Compétitivité (PSPC) des programme d'investissements d'avenir, labélise par plusieurs pôles dont Aerospace Valley.
Jean Luc Bénédini